Impeller Vibration
CFD when applied to fluid machines, allows a realistic insight to the internal pressure and velocity distribution.
Numerous studies have shown that CFD well represents the true flow picture of a machine operating near to its design flow rate. Even when the flow is significantly off-design, this situation still stands. At very low flows, the macroscopic picture is still useful, though not necessarily so accurate. At near to zero flow, the results are least representative, though still useful (Potts and Newton, 1998).
Up until quite recently, CFD has chiefly been used for specific problem solving—at least so far as industrial pumps are concerned. On the other hand, aerospace and military designs could more easily warrant the time and effort expended on analysis prior to testing. However, the ease with which modern codes may be use means that CFD aids are being more and more used alongside traditional methods in the routine design of industrial pumps. This transition mirrors the earlier development in finite element stress analysis.
Previously, the focus has been mainly on the flow patterns and associated losses within the machine. This reflects a natural hypnosis over pump efficiency. However, the flow patterns may also be interpreted in a way that gives clues as to the likely vibration performance of the machine.
Impellers as Hydraulic Vibration Generators
The days have long passed where pump vibrations were viewed as largely a matter of mechanical balance. Nowadays, it is recognized that, even if the pump had near-perfect mechanical balance, it would still exhibit remnant vibrations. The intensity of this remnant vibration turns out to be flow related, with a minimum at or around best efficiency point. Clearly the hydraulic design of the pump has some significance in its vibration behavior.
Why Impeller 1x Vibration is inevitable
Vibration at “one times” shaft rotational frequency is frequently ascribed to driver misalignment or mechanical balance. However, this can also be caused by the impeller if it is machined eccentric to its hydraulic center. The impeller behaves like a hydraulic cam while in the pump, even though it may be in near-perfect mechanical balance in air (Figure 1).
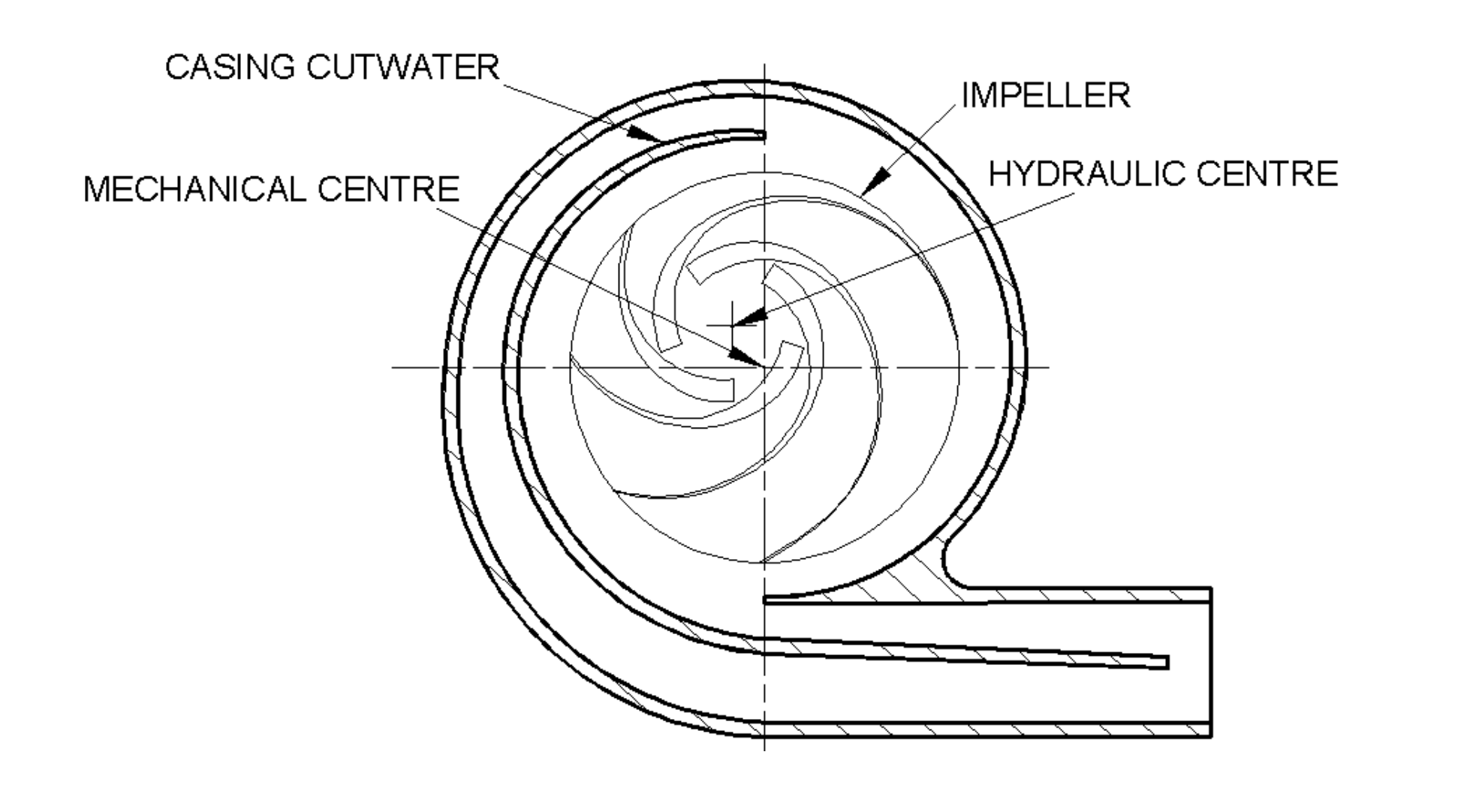
Figure 1. Hydraulic Cam
From a hydraulic design standpoint, vibrations at vane pass frequency are always inherent, due to the way impellers generate head. In order to exert a torque upon the driver, there has to be a pressure differential over each impeller blade. From continuity considerations, this pressure differential results in a velocity difference over both surfaces of the vane. This difference propagates through the passage out into the collector. Thus the collector, and anything connected to it, will experience a fluctuating velocity field once per impeller blade pitch. These result from the turbulent “wake” generated at the trailing edge of the blade, which is fueled by the two different velocity streams mixing out (Figure 2).
In some cases there can also be significant relative velocity changes near mid-pitch, driven by the low energy fluid attached to the low-pressure face of the blade. This mechanism is often idealized into a “jet-wake” model.
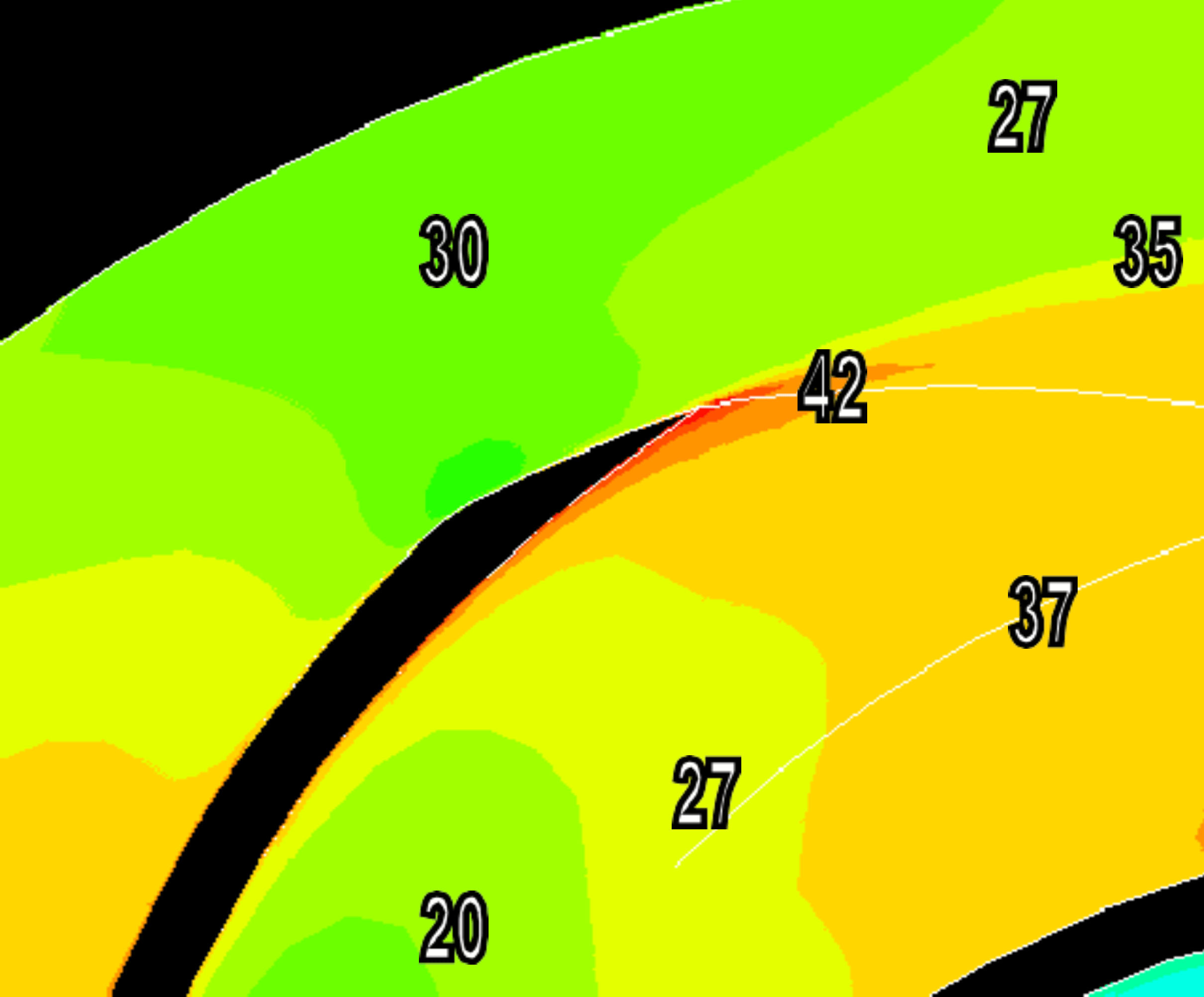
Figure 2. Turbulent Wake at Vane Tip (Absolute Velocity Contours M/Sec).
Designers traditionally attach greatest significance to the relative velocity flows, since this reference framework best helps quantify quality of blade and passage design. However, vibration potential behavior is best described by motion in the absolute reference frame since these are the flows experienced by the casing. Fortunately, discontinuities in the relative reference frame are also reflected in the absolute frame. However most CFD codes will easily show both, so, for review of vibration potential, this is more useful (Figure 3).
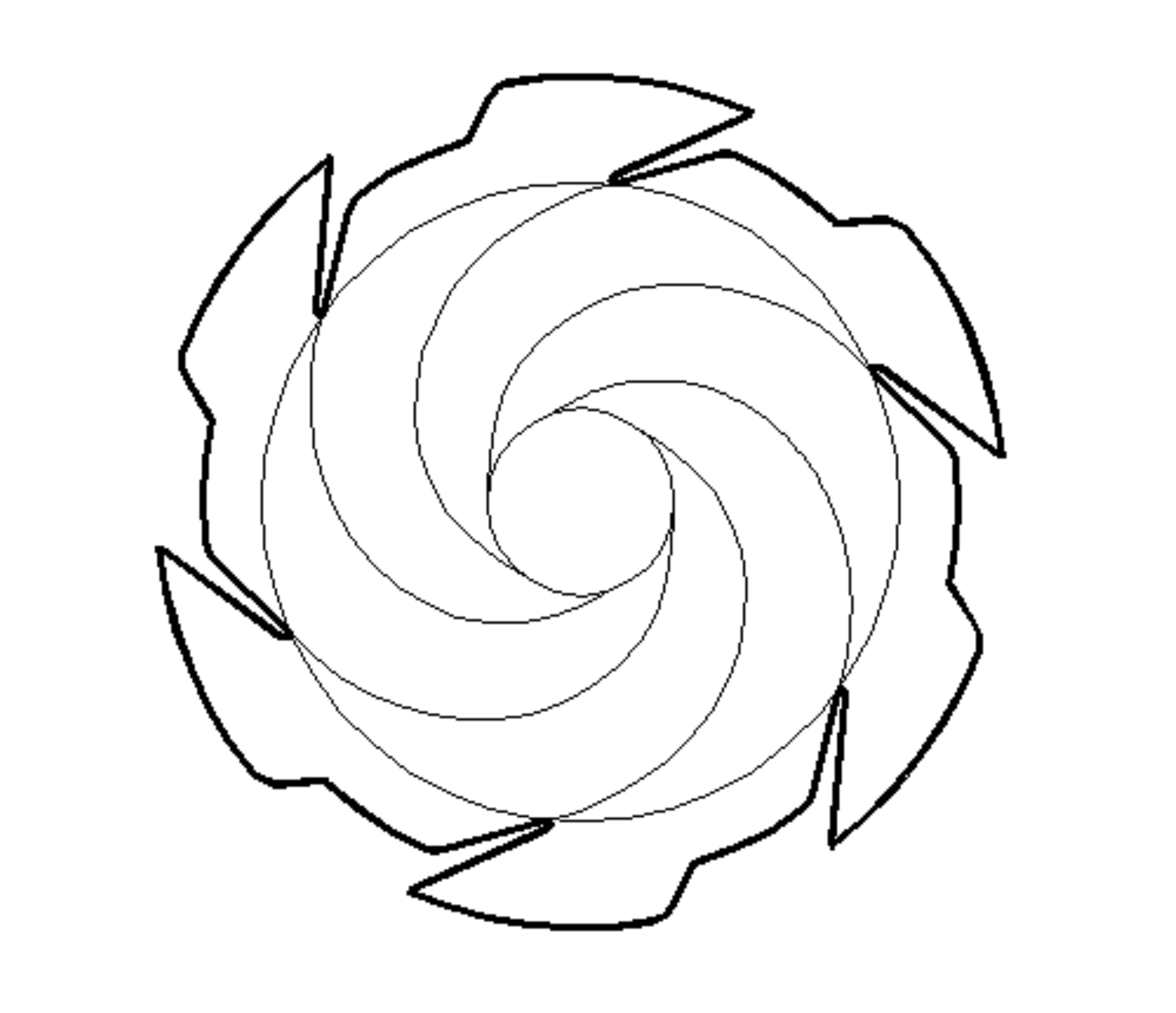
Figure 4. Rotating “Saw Tooth” Pattern in Relative Frame of Reference.
One way of accomplishing this is to increase the physical distance between the impeller and the collector. Wherever two parallel fluid streams of different velocities interface, viscosity effects “mix out” the differences with time/distance. This means that, while the saw tooth pattern measured in the vicinity of the impeller may be quite severe, the intensity diminishes with radial distance. Some pump design specifications, such as API 610 (1995), recognize this and define minimum distances between impeller and casing—in an effort to avoid troublesome vibrations with high-energy pumps. Figure 5 shows how vibration intensity can reduce with distance. While large clearances are one route to low vibrations, it increases machine weight and cost. Most designers of low to medium energy pumps would prefer to select smaller clearances. In any event, the preferred approach should be to attack the problem at the source. This means reducing the vibration potential of the impeller.
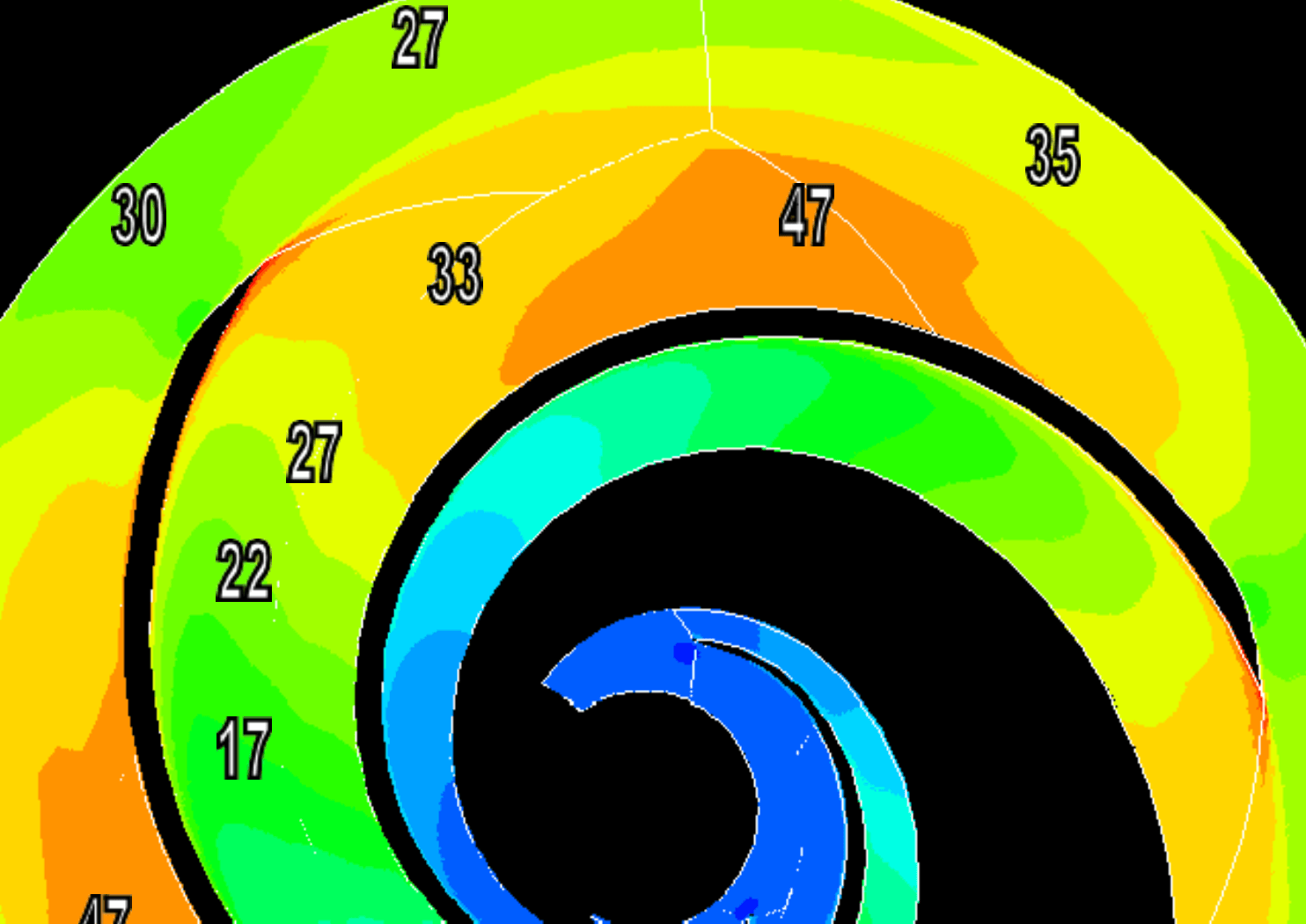
Figure 3. Velocity Distribution Illustrating High Absolute Velocity at Mid-Pitch.
This mid-pitch velocity change may be responsible for vibration at twice vane pass frequency, though mostly lower in intensity than at vane pass. This may be because the casing experiences velocity changes at twice vane pass rate.
Conceptually, these three mechanisms can be represented by a rotating “saw tooth” pattern in the relative reference frame (Figure 4).
Wherever there is a severe change in velocity the machine responds as if to an impulsive force. Evidently, management of velocity changes across each impeller pitch can reduce the severity of these impulses and ultimately the vibration intensity of the machine.
A recapitulation of this section is shown in Table 1
Table 1. Cause and Effect of Impellers as Hydraulic Vibration Generators.
Cause | Effect |
Vibration at once per rev | Hydraulic "cam"effect |
Vibration at vane number per rev | Blade wake effect |
Vibration at twice vane number per rev | Jet-wake effects |
CFD METHODS FOR VIBRATION LEVEL ASSESSMENT
Outlet Velocity Distribution
The mean streamline analysis method is a one-dimensional technique traditionally used in impeller hydraulic design. It will give an indication of fluid velocity between the vanes and midway
across the blade width. No information is yielded regarding the velocity distribution mid-passage or across vane width.
Two-dimensional and quasi-three-dimensional approaches evaluate the blade or passage loading and derive velocities on the blade surfaces. With reference to diffusion criteria, some information regarding velocity distribution may be gained, though at best they yield a crude picture.
Using CFD it is possible to slice through the blade, at any percentage of the width, and inspect the velocity vectors and velocity profile (relative and absolute) (Figure 6).
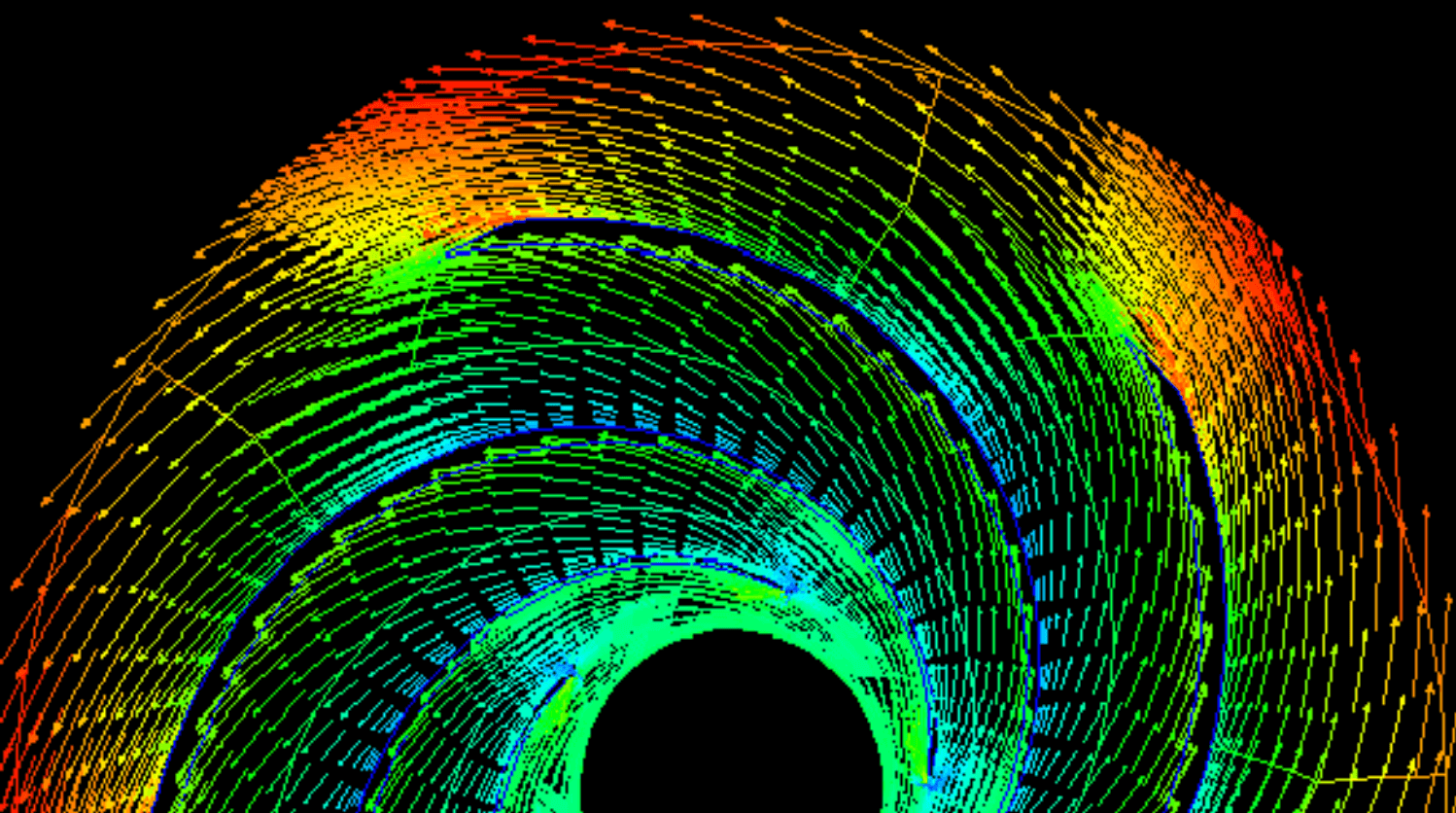
Figure 6. Blade to Blade Relative Velocity Vectors.
This allows “what if” scenarios to be analyzed. Modifications to the hydraulic design will change the outlet velocity profile of the machine. In a qualitative way, these changes can be assessed from a vibration standpoint.
Blade Loading
A blade design, which is heavily loaded, has a high-pressure difference between the front and back surface of the blade. This may produce poor vibration characteristics since a high velocity difference is implicit. Gross separation may even exist, or perhaps stall cells. CFD software now has dedicated processing tools, which allow the designer to access and plot the blade loading data. Designs can be compared and overlaid for direct comparison. Though superficially a backward step, this does allow CFD data to be viewed against a backdrop of traditional 2D and quasi-3D data.
Similarly examining the differences in velocity profiles between the pressure and non-pressure side of the impeller blade gives an indication of the impeller vibration potential.
Complete-Passage Analysis
The impeller flow pattern quality can also have a dramatic effect on vibration levels. Traditional design techniques, many developed from empirical data, often only consider impeller flow at entry and exit in isolation. The stream-wise velocity distribution through a passage cannot be assessed. Passage separation due to local diffusion can be easily identified and eliminated using CFD. Improved management of the flow from inlet to outlet promotes presentation of a more uniform flow field to the collector. This reduces the impeller’s vibration potential (Figure 7).
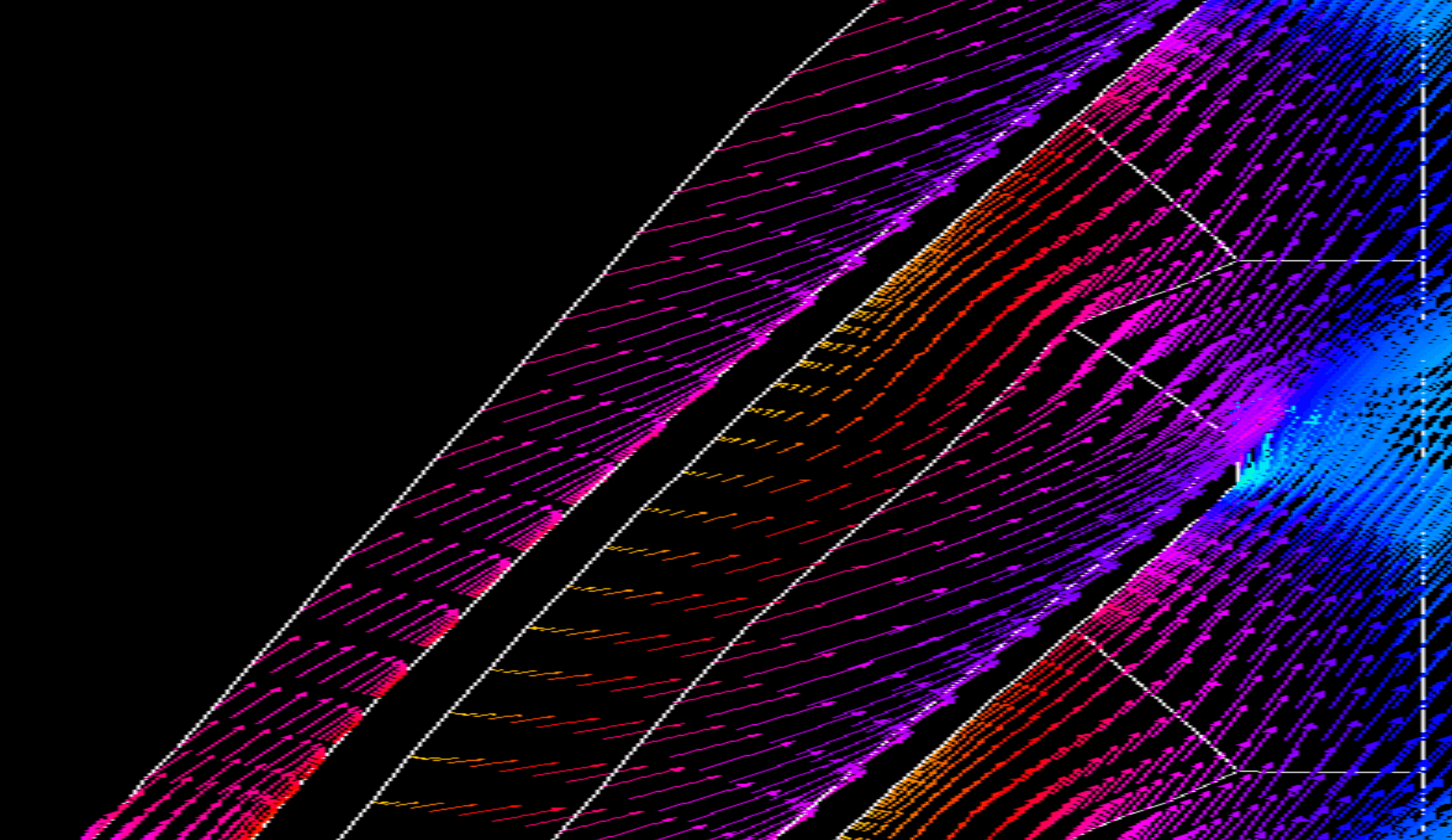
Figure 7. Stall Cell Generation Caused by Poor Impeller Design (Conformal Transformation of Vanes from Polar)
Inlet Backflow
As the flow through the pump is reduced liquid begins to backflow through the impeller inlet out into the inlet duct. Vibration readings taken within this inlet recirculation region will inevitably be high. Recirculating liquid has to exceed the inlet tip velocity in order to escape. This high kinetic energy fluid is dissi- pated either against the inlet pipe wall, or against any discontinuity in the inlet duct, such as bends or straightening ribs.
It has been demonstrated that the impeller inlet geometry, the flow at which zero-incidence occurs, and the inlet tip speed have an influence on the inception of inlet recirculation. Palgrave (1985) presents methods based on empirical data that are often used to predict the point where inlet backflow can be detected. By better controlling the flow at which zero incidence occurs, and the incidence distribution across the inlet edge, it is often possible to ensure the recirculation region is beyond the range of vibration measurement. CFD allows inspection of the incidence at various conditions (Figure 9).
CFD investigation can also be used to ascertain not only the nature of the incidence, but also the nature and effect of the intensity of the inlet backflow. Using CFD it can be ascertained that two distinct zones of fluid interact together within the suction channel.
High-energy liquid is expelled from the impeller eye. This expelled liquid dominates the suction passage, occupying the 2/3 of the flow area from the pipe outer diameter downward toward the channel centerline (Figure 10). The extent that the expelled liquid fills the suction channel remains unchanged with distance from the impeller. This flow spirals helically down the periphery of the suction pipe in a direction counter to the impeller rotation at a constant helical angle.
Each impeller blade generates individual streams. The tangential velocity imposed on the regime by the impeller dominates the flow causing the helical spiral angle to be approximately equal to the
blade inlet angle. This angle does not diminish with distance from the impeller implying that both the tangential and axial compo- nents of the velocity decay proportionally to maintain this angle.
The inner 1/3 of the suction channel area contains a spiraling core of slower moving fluid. Viscous effects transmit tangential energy from the high-energy peripheral flow and drive this core in a helical spiral in the direction of pump rotation. Flow is dominated by the axial component of the velocity and tangential forces exerted by the peripheral flow cause the inner helical flow angle to be approximately double the outer angle. Again the helical spiral angle remains constant.
The interface between the recirculating flow is predicted, by the CFD model, to be 14 multiples of the eye diameter. The position of this interface occurs when the viscous and friction effects have
slowed the net velocity within the channel to zero. This “plugs” the suction pipe, encouraging the outer flow to reverse and form the inner core (Figure 11). The extent that the recirculating flow pushes into the suction duct is linked to the suction peripheral speed of the impeller as proposed by Palgrave (1985) and Fraser (1981). Increasing rotational speed of the impeller or the eye diameter pushes the extent of the recirculation further down the suction passage.
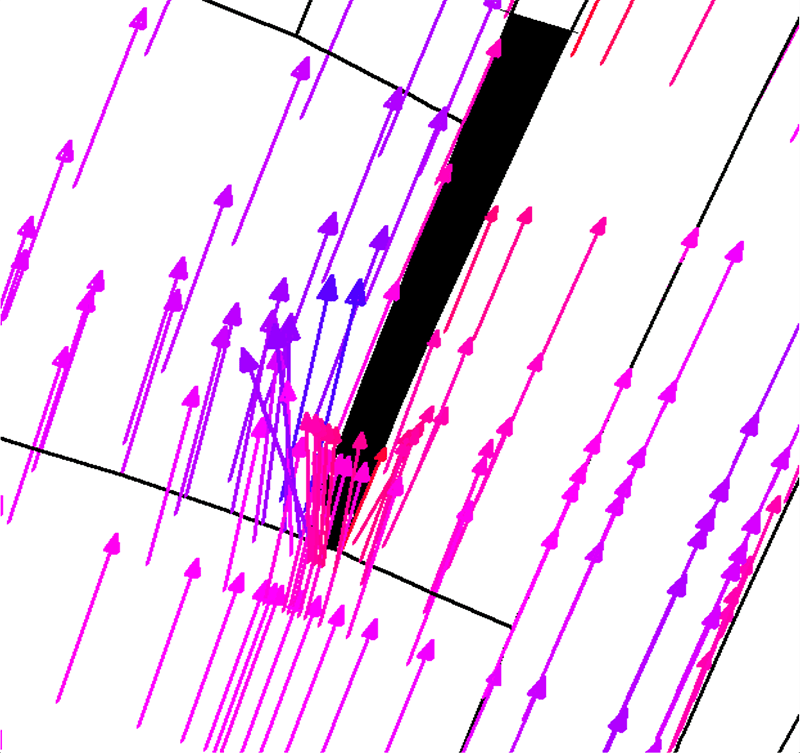
Figure 9. Inspection of Zero Incidence.
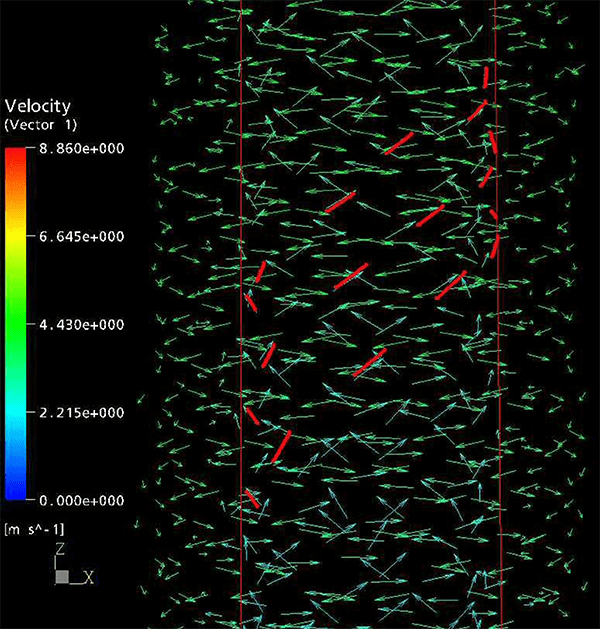
Figure 10. Internal Core of Spiraling Fluid in Suction Channel.
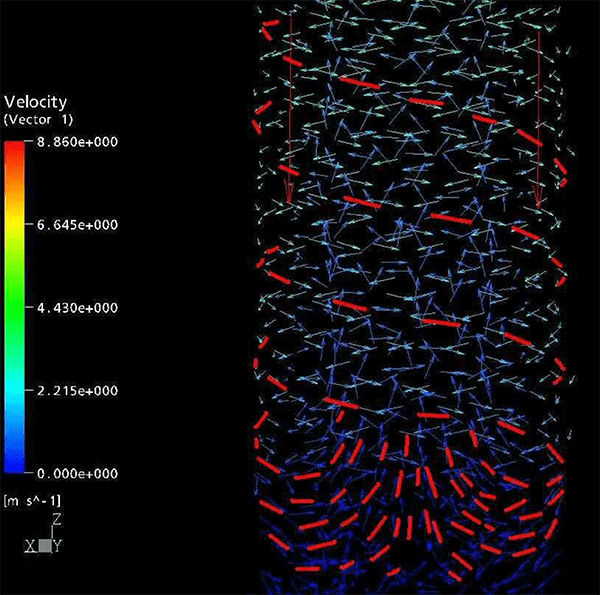
Figure 11. Helical Spiraling Inlet Backflow at Suction Duct Periphery.
The spiraling flow in the suction channel can be used to explain the cyclical vibration often associated with cavitiation surge.
The high energy spiraling outer flow, in the suction channel, has an influence on the incidence condition of the inner core, moving into the impeller, so that the incidence condition deteriorates and intense cavitation occurs. The intensity of this stalls the inlet area between the impeller blade, preventing the outer high energy flow influence on the inner core. As this influence is negated, the incidence recovers and the high-energy spiraling outer proportion is again reinstated.
Using a combination of empirical and computational methods, the inlet backflow recirculation region can be defined closely. Operation in this region leads to high vibration cavitation damage. The phenomenon of cavitation surge is also associated with operation in this region.
SOLUTIONS TO HYDRAULIC VIBRATION
With the information readily available from CFD a design can be “tuned” away from vibration problems by making various changes to the pump geometry, but the vibration can never be completely eliminated.
Discharge Geometry
By changing the vane number and angles and then reevaluating the designs, a balance between hydraulic performance and low vibration potential can be achieved. Typically a combination of low vane numbers and/or high vane outlet angles demonstrates poor vibration characteristics. Such designs are heavily loaded at their tips. However, most commercial pumps are seldom designed purely for low vibration characteristics. High vane angles and increased vane numbers generate more head for a given diameter so their use allows a machine lower in size and cost to be produced.
CFD results can be used as a gauge to help balance the per- formance parameters with the vibration potential of the machine. Qualitative comparisons of impellers with high vane number and low outlet angles can be judged alongside low vane number high outlet angle designs.
Design Comparison Example
To demonstrate the practicality of the method, a machine, which traditionally exhibited poor vibration performance, was redesigned.
CFD analysis methods were used to inhibit the vibration performance of the new design without compromising the pump’s operation and commercial viability.
By comparing the two designs, the features that lead to good vibration design become apparent.
The velocity at jet-wake between the designs is of similar magnitude close to the trailing edge tip but the velocity remains higher and extends further across the blade pitch on the older design. The new design has a quick transition and the velocity streams are mixed out close to the trailing edge.
The original design has a significant velocity peek at mid-pitch on the pressure side of the vane. The comparable peak on the new design has less amplitude and thus a smoother velocity transition (Figure 12). The lowering of this difference reduces the time/distance required for the viscosity effect to “mix out” the streams before they impact on the collector. The vane loading also indicates that this design will generate more head
The vane inlets are lightly loaded, indicating improved net positive suction head (NPSH) performance. Inspection of the vectors at design point indicates that the zero incidence flow for the old design is not at the design flow.
Comparisons of vibration levels taken on test indicate that the acceptable vibration range for the pump has been extended. While the old design of impeller was considered satisfactory on or around its best efficiency flow, its operating range of flows was reduced.
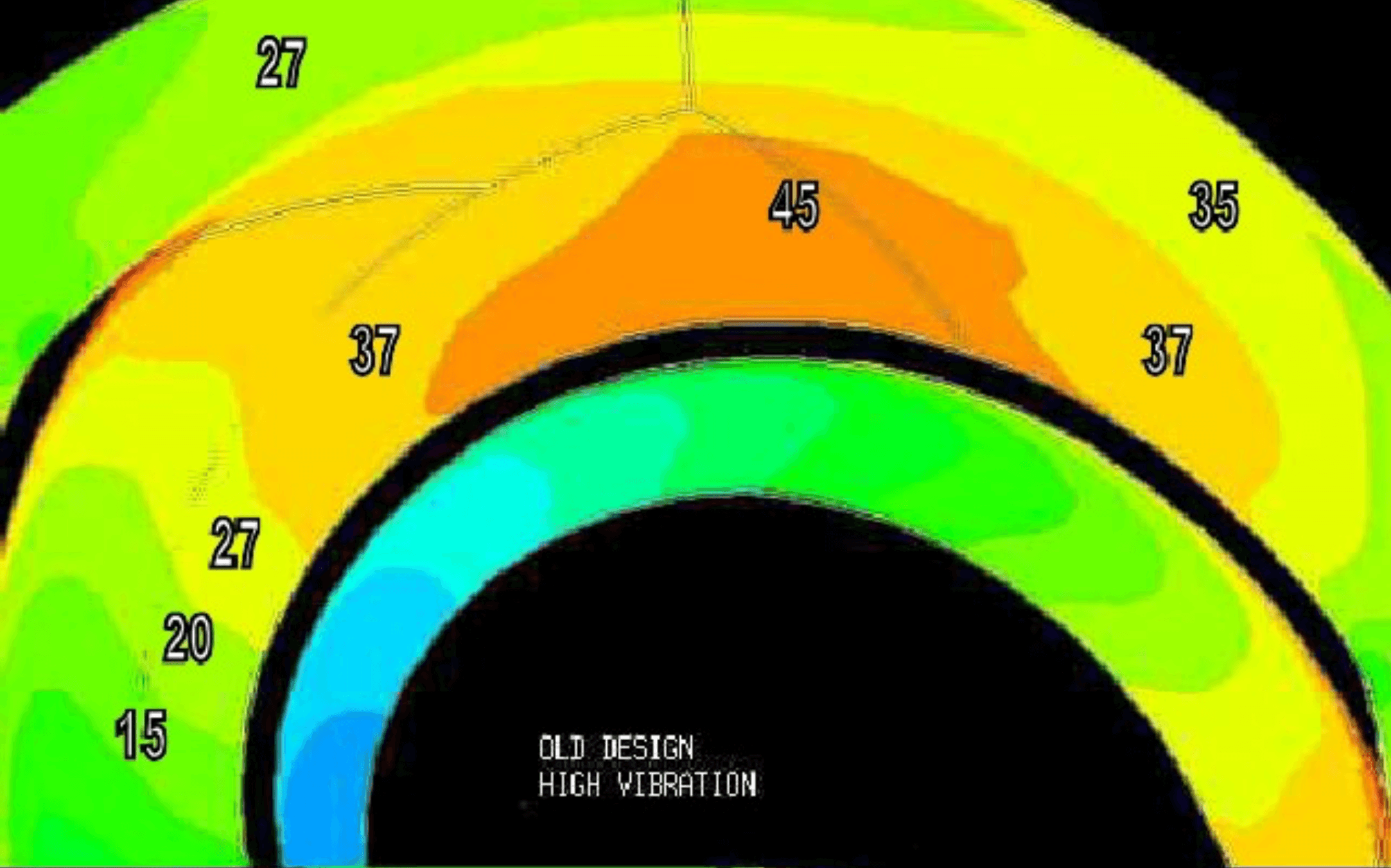
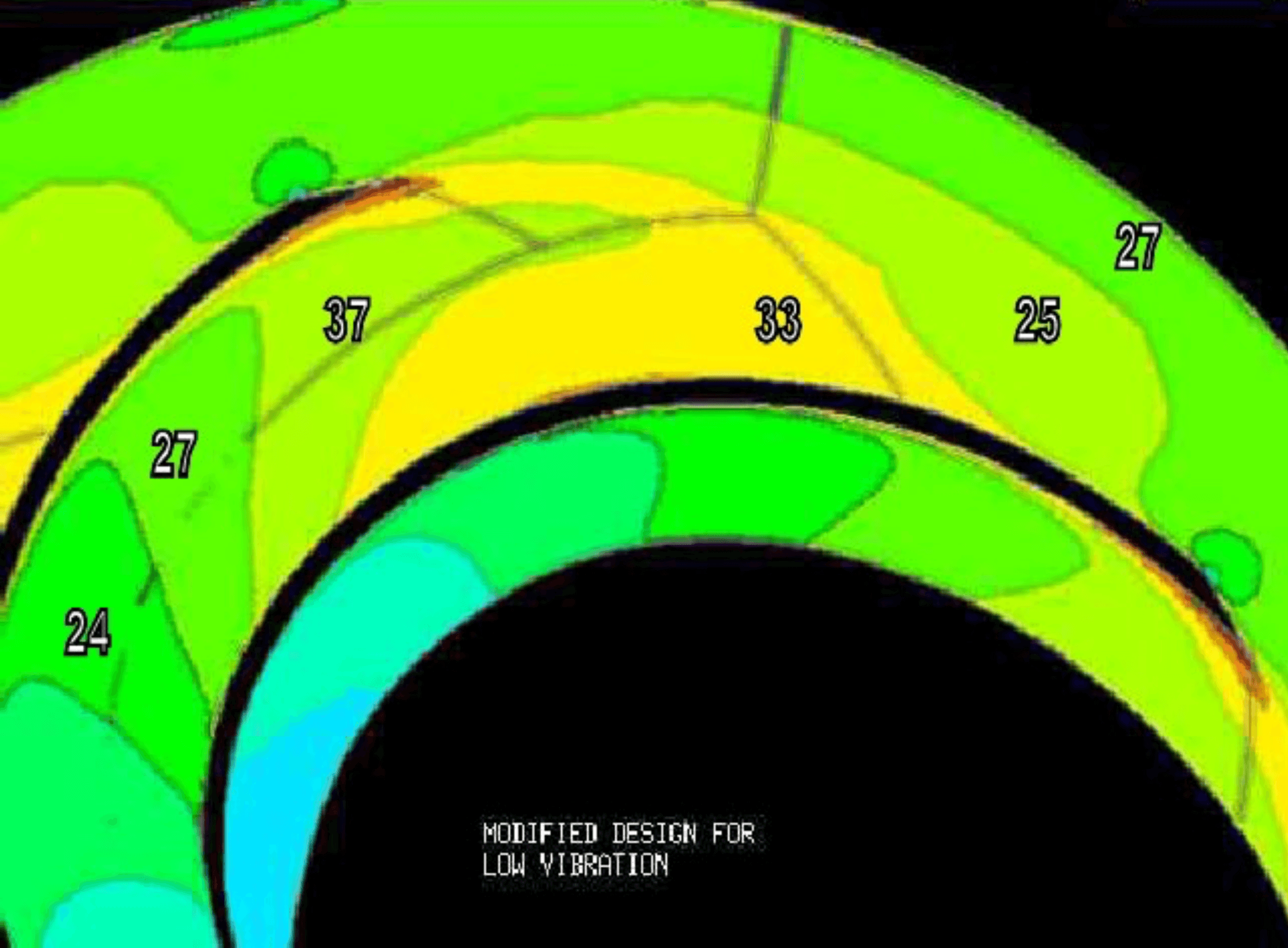
Figure 12. Comparison of Velocity Profiles of One Blade Pitch.
Example 2
Without modifying the discharge vane angle or vane number, it is also possible to control the velocity profile across the vane pitch to reduce vibration levels.
By modifying the blade thickness and inlet incidence one can attempt to control the size, shape, and position of the mid-blade velocity peak. By moving this area further down the blade and smoothing the transition, the velocity will begin to reduce within the boundary of the hub and shroud. This will smooth the velocity peak. As the fluid exits from the impeller, the velocity is a more constant value and as such will excite the casing less (Figure 15).
The high velocity region on the old design at 38 m/s extends beyond the extent of the impeller hub and shroud. The corresponding position on the new design although at a higher velocity is contained within the impeller. When the remnants of this high velocity region reach the impeller periphery they have slowed so that the velocity over one pitch is virtually constant (Figure 16).
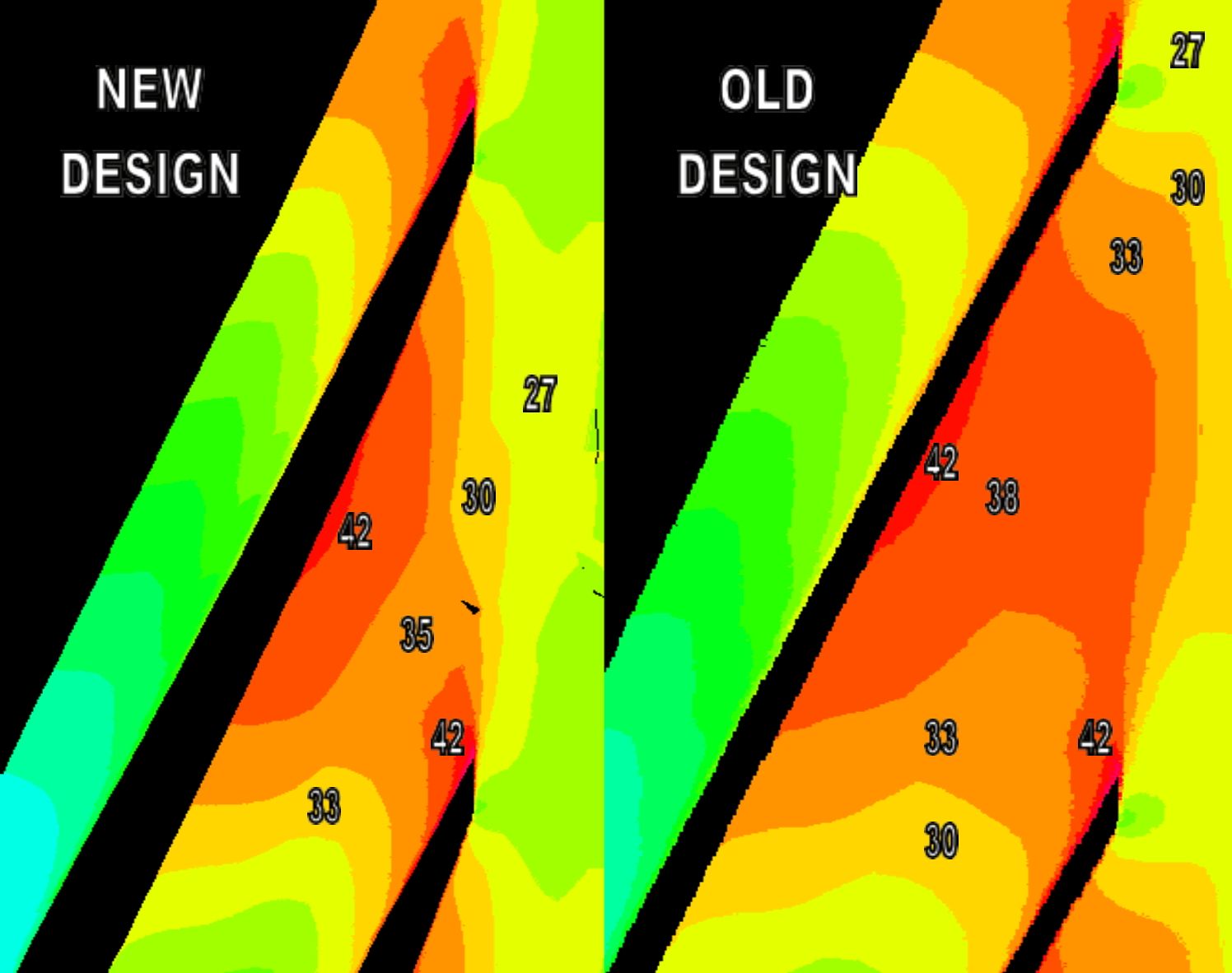
Figure 15. Absolute Velocity Profile Comparison across One Blade Pitch.
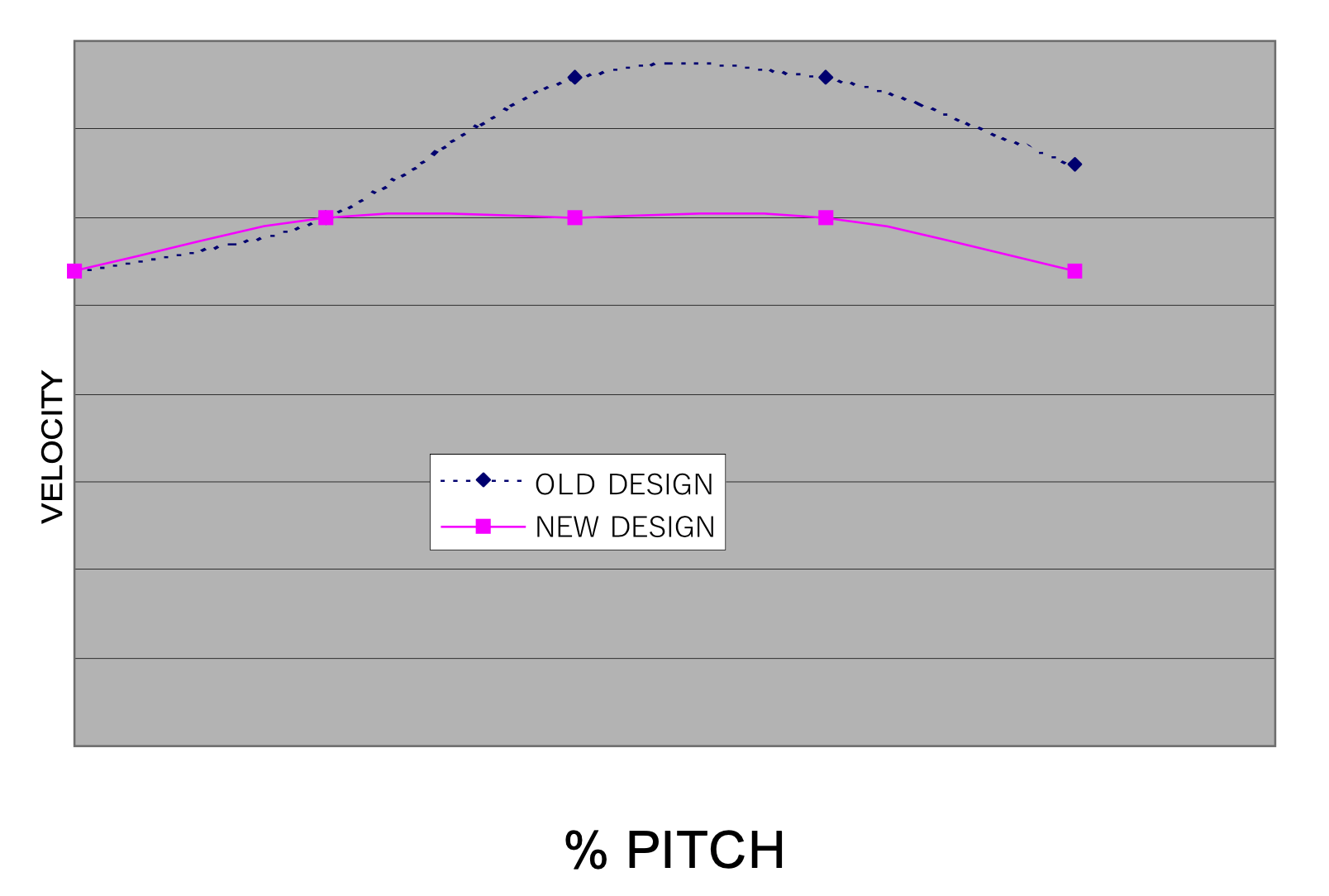
Figure 16. Velocity at Impeller Periphery across One Blade Pitch.
VELOCITY
Simple Vane Considerations
Pressure pulsations at vane frequency are initiated by the each vanes of the impeller passing close to the volute cutwater lip.
These pulsations can have a great consequence on the vibration of the machine. Traditional methods to reduce these pressure pulsations involve increasing the distance between the impeller vanes and lips to allow time, distance and viscosity to smooth out this pressure wave. Unfortunately this technique does not come without penalty and has a consequence to both head and efficiency.
To reduce the pressure pulsation without impacting adversely the machine hydraulic performance Hydro designed and installed staggered and raked vanes to the impeller. This requires a center rib to be designed into the impeller around which the impeller vanes can be staggered. This means that the vane tip width passing the cutwater is halved in length and the rake angle of the blade spreads this passing over a greater time/distance.
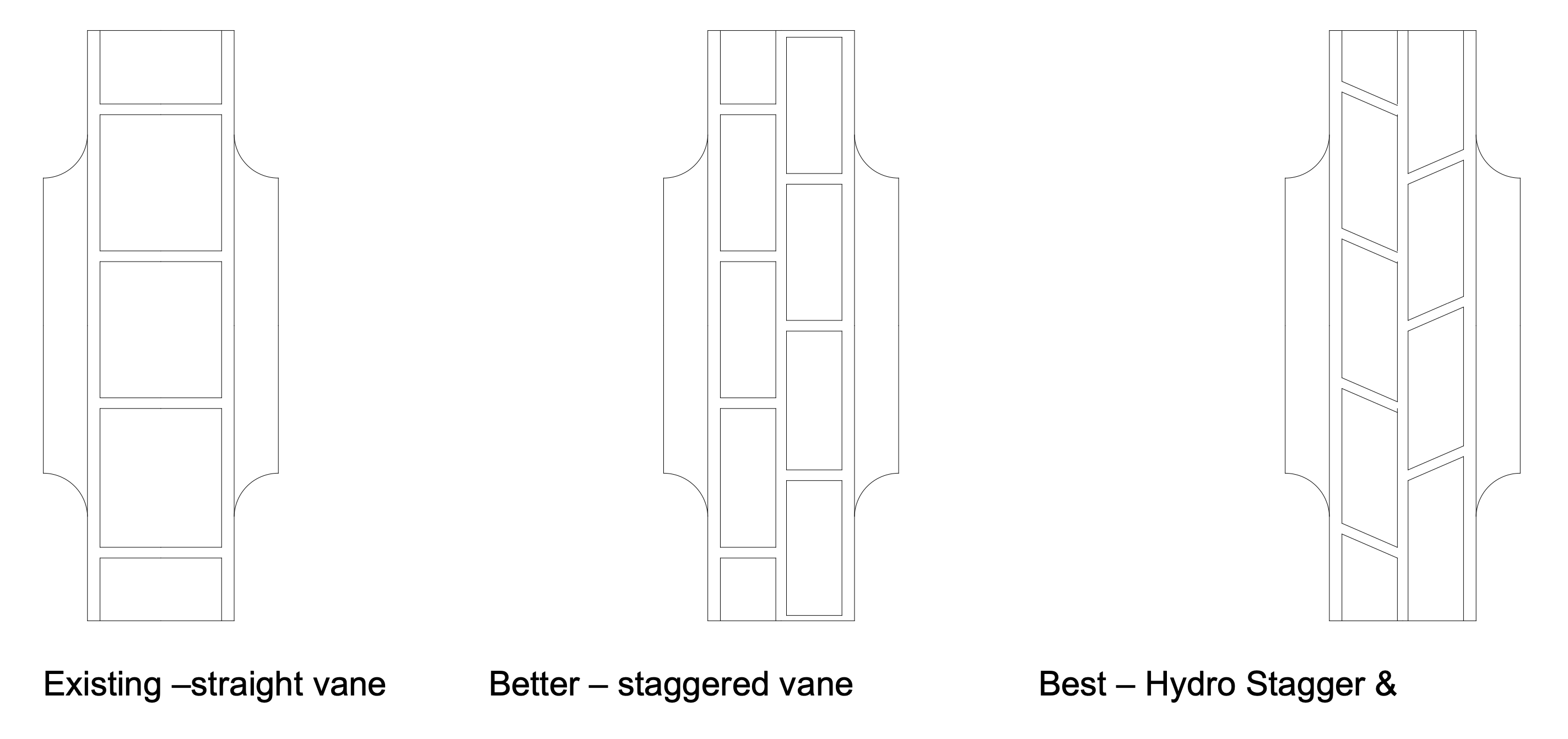
Existing –straight vane Better – staggered vane Best – Hydro Stagger &
Essential Take Away
- Vane Pas Vibration is inevitable – Management of the design provides improvements
- Large tip clearance allowing time/distance/viscosity to slow the velocity from impeller to collector limit vane pass but also mean machines are larger and less efficient
- Providing a longer raked blade profile to the collector can reduce vane pass
- Higher loaded forced head impellers have higher vibration potential
- Long blades with high solidity help reduce vibration
- CFD as an indicator of vibration potential is not an absolute quantitative method but a system of ranking designs and refining geometry so that the consequences of each actual design are under- stood from a vibration standpoint.
- This analysis system only considers the impeller in isolation and is not truly representative of the flow within the machine. The collector has an influence on the impeller flow field. At design flow this influence is small as concluded by Miner (1988). Considering the impeller in isolation is an appropriate method where solutions can ranked against each other.
- The solution of off-design problems to assess the influence of the inlet backflow recirculation is a much longer process. The flow pattern is considered to change as the influence of the casing has a different effect at every position of the blade in relation to the casing tips.
- Using CFD analysis in conjunction with best practice mechanical design it is possible to reduce vibration levels at off-design flows by designing the impeller to more closely match the operating condition of the pump. This allows the pump user to improve the reliability of the seals and bearings, while retaining flexibility of operation.
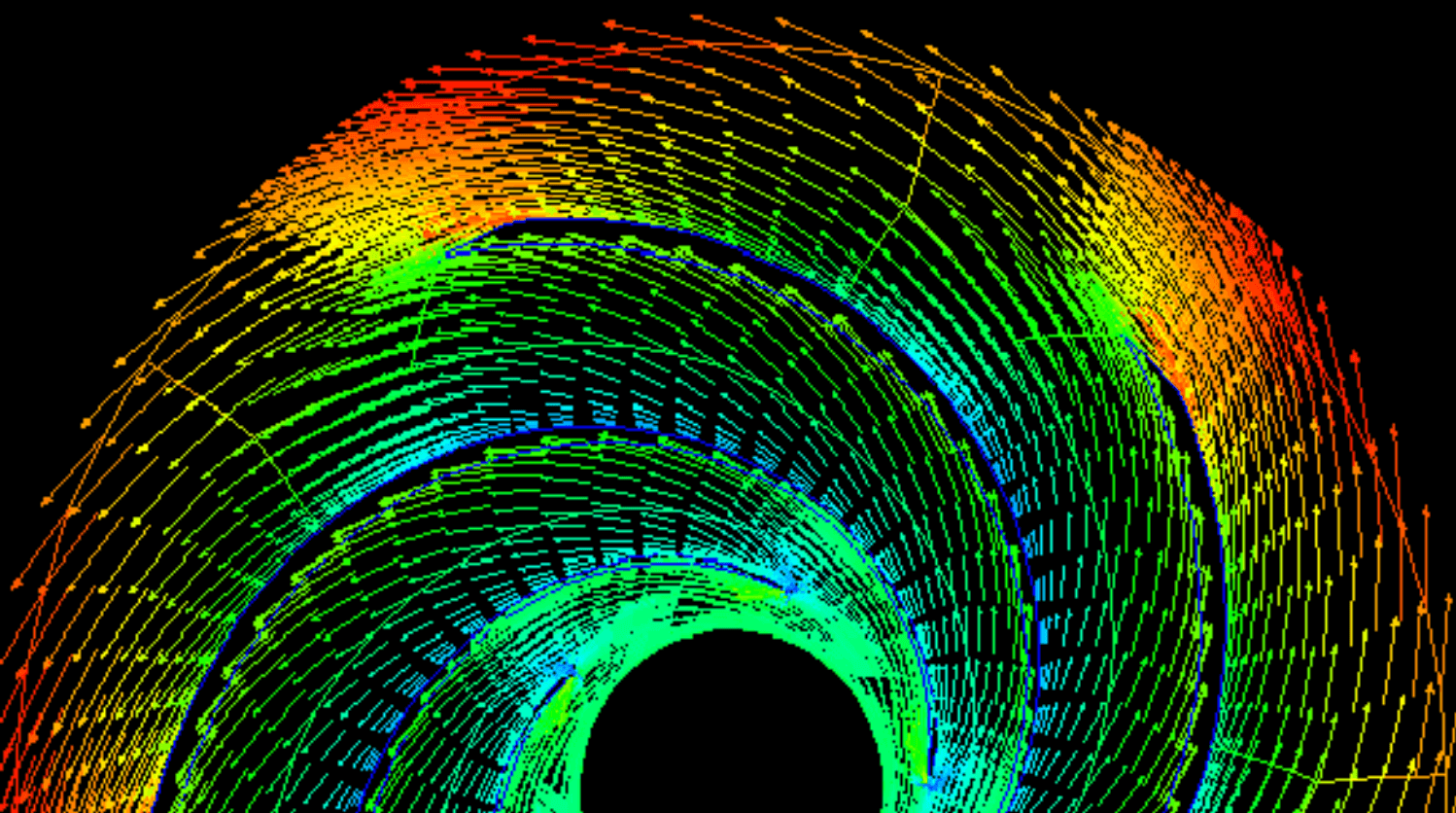
More Recent Articles
-
Pump Efficiency: Half the Story?
It is an insightful practice to view pump efficiency as a combination of 3 factors ...
Mechanical Efficiency: The amount of mechanical power required to turn the rotor and overcome friction ...
More
-
Mechanical Balance
It is common in centrifugal pumps to balance the rotating components to an internationally recognised ...
Many companies have overarching methodologies that define the procedure as:
Balance individual components, generally on a ...More